Polyurethane Foam
Why Consider a Polyurethane Foam Roof Coating Application?
Polyurethane foam must be recoated every 10 years or so as a preventive measure.
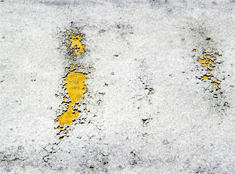
BEFORE: This 10 year old polyurethane foam roof is badly weathered. Some of the foam is already exposed.
Polyurethane Foam Roof Restoration Process
Cleaning and Surface Preparation
The entire polyurethane roof was thoroughly washed using a 3,000 psi pressure washer. A biodegradeable degreaser was used to ensure a clean surface. All seams, flashings and penetrations were carefully sealed to render the roof watertight.
Priming
Priming ensures a good adhesion between the polyurethane foam roof surface and the
elastomeric coating.
Top Coating
At least 30 dry mils of elastomeric roof coating is applied on the entire polyurethane foam roof in 2 coats.
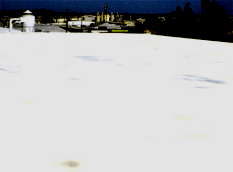
AFTER:
A leak-free, seamless elastomeric roofing membrane now covers the old, weathered polyurethane foam roof. If this polyurethane foam roof is properly maintained with periodic recoating, it can have an indefinite life expectancy.
All these benefits for about half the cost of replacement. What more can you ask for?
I. PRODUCTS
1.01 FIXALLROOF RESTORATION SYSTEM
- The elastomeric roofing system for polyurethane foam roofing is a spray-applied roof coating supplied by epdmcoatings.Product Acrylic System Solvent System
PrimeLock Primer Bonding Primer Seam Products PolyScrim Roofing Fabric
Acrylic Elastomeric CaulkPolyScrim Roofing Fabric
Butyl Rubber CaulkBase Coat / Top Coat Acrylic Elastomeric Coating Butyl Rubber Coating
Aromatic Urethane Coating
Silicone Coating
1.02 PRODUCT SUBSTITUTIONS
-
Use Butyl Rubber Coating, Aromatic Polyurethane Coating or Silicone Coating instead of PrimeLock Bonding Primer as the adhesive for PolyScrim when installing the Solvent Based System.
1.03 RELATED MATERIALS
-
Roof accessories, flashing, seam tapes and similar materials shall be approved by the manufacturer. All materials used shall be applied in accordance with its manufacturer’s recommendations.
1.04 EQUIPMENT
-
Visit the Fixallroof website for recommended spray equipment guidelines, or consult the spray equipment manufacturer directly.
II. EXECUTION
2.01 MANUFACTURER’S INSTRUCTIONS
-
Comply with the instructions and recommendations of the roof restoration system manufacturer.
-
Comply with manufacturer’s product data, including product technical bulletins.
2.02 EXAMINATION
-
Verify conditions are acceptable for application of roof restoration system .
-
Inspect polyurethane foam roof to receive roof coating and make sure they are clean, sound, properly prepared and free of moisture, dirt, debris or other contaminants.
-
A comprehensive moisture survey is to be conducted to locate and identify areas of trapped moisture and saturated insulation.
-
Verify that all on-roof items, penetrations, mechanical equipment, hvac drains are in place and secure. All airconditioning and air intake vents should be suitably protected or closed.
-
Verify that areas within the vicinity of the application area as protected from overspray.
-
Verify that all roof drains, gutters, downspouts, catch basins are clean and in working order.
2.03 PREPARATION
-
Cleaning: The entire polyurethane foam roof surface must be clean, sound, dry and free of any contaminants that would interfere with the proper adhesion of the roof coating. This may require pressure washing, scraping, wire brushing or other means necessary while observing responsible trade practices. All loose paint should be removed before applying any product.
-
Ponding Water: Contractor shall make every effort to mechanically eliminate all ponding water areas on the polyurethane foam roof prior to application of any roof coating product.
-
Repairs: Wet roof insulation and damaged membranes are to be removed and replaced as necessary to match existing specified material. All ponds that hold water over 1″ for more than 48 hours should be mechanically diverted.
-
Blisters: Remove all wet foam and repair all blisters in accordance with polyurethane foam roof manufacturer’s specifications.
-
Do not apply coatings until all unsatisfactory conditions have been corrected in a manner acceptable to the original polyurethane foam roofing manufacturer.
2.04 APPLICATION
-
Inspect polyurethane foam roof to receive roof coating. Always perform a coating adhesion test before doing the entire job.
-
Primer: Entire polyurethane foam roof shall be primed using the appropriate primer and following the application rates specified in the table below.
-
Seams: All seams, penetrations and parapet walls should be flashed using PolyScrim Fabric and PrimeLock Bonding Primer. Apply a thin coat of PrimeLock Bonding Primer over the seam and roll out 6″ fabric over the seam and apply another coat of PrimeLock Bonding Primer over the fabric. Encapsulate the fabric with the appropriate elastomeric coating and feathering it at least 2″ to 3″ past the edge of the fabric. Substute PrimeLock Bonding Primer with the appropriate topcoat as outlined in 2.02 above.
-
Base Coat: Apply appropriate base coat using the application rates specified in the table below. Allow to dry thoroughly for 8-12 hours depending on humidity and temperature.
-
Top Coat: Apply appropriate top coat in a cross-hatch technique using the application rates specified in the table below. Allow to dry and cure before exposing to foot traffic.
-
Standard System: Use the Acrylic System on polyurethane foam roofs with good slope and no ponding water issues. Use the Solvent System when outdoor temperatures are no longer favorable for acrylic coatings.
Acrylic System Primer Base Coat Top Coat
Acrylic System Primer Base Coat Top Coat Polyurethane Foam
Standard System
5-year (32 total mils)PrimeLock Bonding Primer
0.75 gal. / 100 s.f.Acrylic Elastomeric Coating
1.50 gal. / 100 s.f.Acrylic Elastomeric Coating
1.50 gal. / 100 s.f.Polyurethane Foam
Standard System
10-year (40 total mils)PrimeLock Bonding Primer
0.75 gal. / 100 s.f.Acrylic Elastomeric Coating
2.00 gal. / 100 s.f.Acrylic Elastomeric Coating
2.00 gal. / 100 s.f.Solvent System Primer Base Coat Top Coat Polyurethane Foam
Standard System
10-year (36 total mils)Aromatic Polyurethane Coating
1.50 gal. / 100 s.f.Aromatic Polyurethane Coating
1.50 gal. / 100 s.f.Polyurethane Foam
Standard System
10-year (36 total mils)Silicone Coating
1.75 gal. / 100 s.f.Silicone Coating
1.75 gal. / 100 s.f.Polyurethane Foam
Standard System
10-year (36 total mils)Butyl Rubber Coating
2.50 gal. / 100 s.f.Butyl Rubber Coating
2.50 gal. / 100 s.f.
2.05 FIELD QUALITY CONTROL
-
Utilize manufacturer’s field services to verify proper installation of the system. Areas that do not meet the minimum standards for application specified herein shall be corrected at the contractor’s expense. Manufacturer’s inspection or verification shall not constitute acceptance of responsibility for any improper application of material.
2.06 CLEANING
-
Surfaces not to be coated shall be protected during the application of the system. If protection is not feasible, surfaces shall be restored to their proper condition by cleaning, repairing or replacing.
-
In conjunction with the final inspection, all debris, containers, materials and equipment are to be properly removed from the job site. Grounds are to be cleaned undamaged and acceptable to the owner.
-
Dispose of all containers in accordance with state and local environmental regulations.
-
Reflectivity of coatings may be reduced if roof surface is not cleaned regularly.
2.07 PROTECTION
-
Control overspray especially during windy conditions.
-
All parking areas adjacent to (within 75 feet) the work area are to be cleared and roped off.
-
Protect work from damage due to subsequent construction activity on the site.
-
Roof coatings are not traffic grade. Areas surrounding roof top equipment may be reinforced by embedding PolyScrim fabric and applying a thicker membrane (40-50 mils). Walk pads should be used if frequent maintenance traffic is expected.